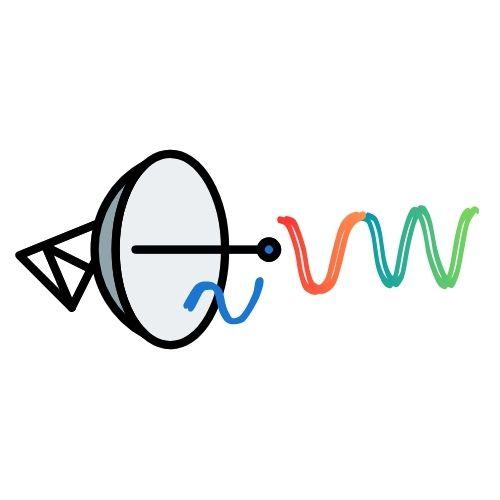
-
StatusCompleted
-
Status date2024-03-25
-
Activity Code6A.077
Very High Throughput Satellite systems are shifting towards Q/V/W-band for the feeder link due to rapidly increasing traffic demand. These new bands provide larger usable spectrum while freeing Ka-band for the increasingly demanding user connectivity. However, the manufacturing of waveguide feeders at these bands become increasingly complex due to the shrinking feature size. Conventional milling techniques require tool access, so the components must be machined out of multiple piece-parts that are connected using flanges and screws. This results in bulky assemblies, which impacts on insertion losses and eventually system performance.
This activity addresses this challenge by applying high-precision 3D printing techniques to produce monolithic components with much reduced interfacing and assembly. The project also explores the full design flexibility afforded by 3D printing.
The University of Birmingham partners with Airbus, who has heritage Q/V-band development, and Filtronic, who has commercial production experience with V/W band components. This activity develops and validates three breadboards of fully integrated passive waveguide feeders at Q, V and W-band, respectively.
The technical specifications for the hardware are stringent in terms of the requirement for dual circular-polarisation separation over either a wide band or two widely distanced frequency bands. There are significant trade-offs among bandwidth, polarisation isolation and frequency multiplexing.
The other challenge area is the manufacture. Polarisers, orthomode transducers and multiplexers are known to be hard to manufacture and sensitive to imperfections in both manufacture and assembly. This activity explores the use of additive manufacture (AM) techniques. Design-for-manufacture is an important consideration to take advantage of the free-forming capability of AM without sacrificing the RF performance.
This is a technology development activity that ultimately enables the delivery of new and enhanced services primarily for high throughput satellite systems.
Specifically, the activity delivers highly integrated and compact ground feeders, as key components in gateway link systems. This supports the rapid development of new gateway infrastructure over new and higher frequency bands in the Europe.
Moving to a compact solution for the waveguide feeder, enabled by new manufacture techniques, offers significant benefit in term of front-end efficiency (reducing losses and improving noise and transmit power) and ease of assembly and integration.
The main product features include:
-
Hardware with reduction of number of piece-parts by at least a factor of 2;
-
Reduction of insertion losses in the order of 0.5-2 dB as a result of the reduced RF interfaces;
-
Reduction of effort in assembly, integration and testing;
-
Antenna feeders with advanced functions for Q/W and V/W bands that have not been fully explored before.
All are enabled by the free-forming capability of additive manufacture techniques and new designs that take advantage of these new manufacture process.
The activity develops hardware components for three different band combinations. The architecture for each depends on the specific polarisation and multiplexing requirements. The hardware contains polarisers, orthomode transducers, filters, diplexers or multiplexer.
The project has six technical work packages:
WP1000: Finalised Technical Specification
WP2000: Technology Selection
WP3000: Detailed Design of Prototypes
WP4000: Implementation and Verification Plan
WP5000: Verified Deliverable Items and Compliance Statement
WP6000: Technology Assessment and Development Plan
The Q/V band hardware development is in parallel with the Q/W and V/W band development.
There are four milestones:
MS1: Finalised technical specification and technology selection
MS2: Detailed design and implementation & verification plan
MS3: Test results and assessment
MS4: Final report
The KO meeting of the project took place in December 2023.